Industrial Injection: The Backbone Of Modern Manufacturing
Industrial injection has become one of the most critical processes in modern manufacturing. Imagine a world where products are produced seamlessly, with precision and efficiency. That's exactly what industrial injection brings to the table. Whether it's plastic components for electronics or intricate molds for automotive parts, this process plays a pivotal role in shaping industries worldwide. So, if you've ever wondered how your favorite gadgets or car parts are made, keep reading because we're about to dive deep into the fascinating world of industrial injection.
Now, let's break it down for you. Industrial injection is not just some fancy term thrown around in manufacturing circles. It's a process that involves injecting molten material into a mold cavity to create specific parts. This technique is widely used across various industries because of its ability to produce complex shapes with high precision and repeatability. Think of it as the secret sauce that makes mass production possible without compromising quality.
But why does industrial injection matter so much? Well, it's all about efficiency, cost-effectiveness, and scalability. In today's fast-paced world, businesses need to churn out products quickly while maintaining top-notch quality. Industrial injection allows manufacturers to do just that. From small-scale operations to large-scale productions, this process offers flexibility and adaptability, making it an indispensable tool in the manufacturing toolkit.
What Exactly is Industrial Injection?
Let's get into the nitty-gritty of industrial injection. At its core, this process involves melting raw materials, usually plastics, metals, or composites, and injecting them into a mold under high pressure. The molten material fills the mold cavity, taking on its shape as it cools and solidifies. This might sound simple, but there's a lot of science and engineering that goes into making it work flawlessly.
Industrial injection machines come in various sizes and configurations, depending on the application. From small benchtop machines for prototyping to massive industrial units capable of producing thousands of parts per hour, there's a machine for every need. These machines are equipped with advanced control systems that ensure consistent quality and minimize defects. It's like having a robot that can replicate your designs with pinpoint accuracy.
Key Components of Industrial Injection
Every industrial injection setup consists of several key components that work together to produce the desired results. Here's a quick rundown:
- Why Miss Steak Is Every Foodies Dream Come True
- Dove Y Damiano The Ultimate Guide To Love Relationships And Modernday Romance
- Injection Unit: This is where the raw material is melted and injected into the mold.
- Mold: The mold defines the shape and dimensions of the final product. It's usually made of steel or aluminum and can be customized to meet specific requirements.
- Clamping System: This part holds the mold in place during the injection process, ensuring that the molten material doesn't leak out.
- Control System: Modern injection machines are equipped with sophisticated control systems that monitor and adjust various parameters to optimize performance.
Each of these components plays a crucial role in the overall process, and their proper functioning is essential for achieving high-quality results. Think of them as the building blocks that make industrial injection possible.
Applications of Industrial Injection
Industrial injection finds applications in virtually every industry you can think of. From automotive to electronics, healthcare to consumer goods, this process is used to produce a wide range of products. Let's take a closer look at some of the most common applications:
Automotive Industry
In the automotive sector, industrial injection is used to produce everything from small components like dashboard buttons to large parts like bumpers and door panels. The ability to create complex shapes with high precision makes it ideal for this industry. Plus, the use of lightweight materials like plastics helps reduce vehicle weight, improving fuel efficiency.
Electronics Industry
When it comes to electronics, industrial injection is used to produce housings, connectors, and other components. The process allows manufacturers to create intricate designs with tight tolerances, ensuring that each part fits perfectly with the rest of the assembly. It's like putting together a puzzle where every piece has to fit just right.
Healthcare Industry
In healthcare, industrial injection is used to produce medical devices, surgical instruments, and even prosthetics. The ability to maintain strict quality control and sterilization standards makes it a preferred choice for this industry. Whether it's a syringe or a pacemaker, industrial injection ensures that every product meets the highest standards of safety and reliability.
The Science Behind Industrial Injection
Now that we know what industrial injection is and where it's used, let's dive into the science behind it. The process involves several key steps, each of which is crucial for achieving the desired results. Here's a breakdown of the process:
Melting the Material
The first step in industrial injection is melting the raw material. This is done using an injection unit, which heats the material to its melting point. The temperature and pressure settings are carefully controlled to ensure that the material flows smoothly and fills the mold cavity evenly.
Filling the Mold
Once the material is melted, it's injected into the mold under high pressure. The pressure ensures that the material reaches every corner of the mold, creating a perfect replica of the desired shape. This step is critical for achieving high-quality results, as any defects or air bubbles can compromise the final product.
Cooling and Solidification
After the mold is filled, the material is allowed to cool and solidify. This step is where the magic happens, as the molten material transforms into a solid part. The cooling process is carefully controlled to prevent warping or other defects that could affect the part's performance.
Ejecting the Part
Once the part has cooled and solidified, it's ejected from the mold using a mechanical system. This step is automated in most modern injection machines, ensuring that the process is efficient and consistent. The ejected part is then inspected for quality before being sent for further processing or assembly.
Challenges in Industrial Injection
While industrial injection is a powerful tool, it's not without its challenges. Manufacturers face several hurdles when implementing this process, from material selection to quality control. Here are some of the most common challenges:
- Material Selection: Choosing the right material for a specific application can be tricky. Factors like temperature resistance, flexibility, and durability must be carefully considered.
- Design Constraints: Not all designs are suitable for industrial injection. Complex geometries or thin walls can pose challenges that require specialized molds or materials.
- Quality Control: Ensuring consistent quality across large production runs is a major challenge. Defects like warping, shrinkage, or surface imperfections can occur if the process isn't properly controlled.
Overcoming these challenges requires a combination of expertise, advanced technology, and rigorous testing. It's a constant balancing act between efficiency and quality, but the rewards are well worth the effort.
Advancements in Industrial Injection
As with any technology, industrial injection continues to evolve and improve. Advances in materials science, machine design, and automation are pushing the boundaries of what's possible. Here are some of the latest trends in the field:
Smart Machines
Modern injection machines are equipped with sensors and AI-driven systems that monitor and optimize the process in real time. These "smart machines" can detect defects, adjust parameters, and even predict maintenance needs, improving efficiency and reducing downtime.
New Materials
Researchers are constantly developing new materials with improved properties, such as increased strength, flexibility, or sustainability. These materials are opening up new possibilities for industrial injection, enabling manufacturers to create products that were once thought impossible.
Sustainability
With growing concerns about environmental impact, the industry is shifting towards more sustainable practices. This includes using recycled materials, reducing energy consumption, and minimizing waste. It's a win-win for both manufacturers and the planet.
Industrial Injection in the Future
Looking ahead, the future of industrial injection looks bright. As technology continues to advance, we can expect even more innovations that will transform the manufacturing landscape. Imagine machines that can produce parts on demand, with zero waste and minimal energy consumption. Or materials that can heal themselves, extending the lifespan of products and reducing the need for replacements.
These possibilities are no longer science fiction but are becoming a reality thanks to the relentless pursuit of innovation. Industrial injection will undoubtedly play a key role in shaping the future of manufacturing, driving progress and growth across industries.
Conclusion
Industrial injection is more than just a manufacturing process; it's a cornerstone of modern industry. From its humble beginnings to the advanced systems we see today, this technology has come a long way. It offers unparalleled precision, efficiency, and scalability, making it an indispensable tool for manufacturers worldwide.
So, whether you're a business owner looking to optimize your production processes or simply curious about how things are made, industrial injection is definitely worth exploring. And who knows? Maybe one day you'll find yourself at the forefront of the next big innovation in this exciting field.
Don't forget to share your thoughts in the comments below and check out our other articles for more insights into the world of manufacturing. Until next time, stay curious and keep learning!
Table of Contents
- What Exactly is Industrial Injection?
- Key Components of Industrial Injection
- Applications of Industrial Injection
- The Science Behind Industrial Injection
- Challenges in Industrial Injection
- Advancements in Industrial Injection
- Industrial Injection in the Future
- Conclusion
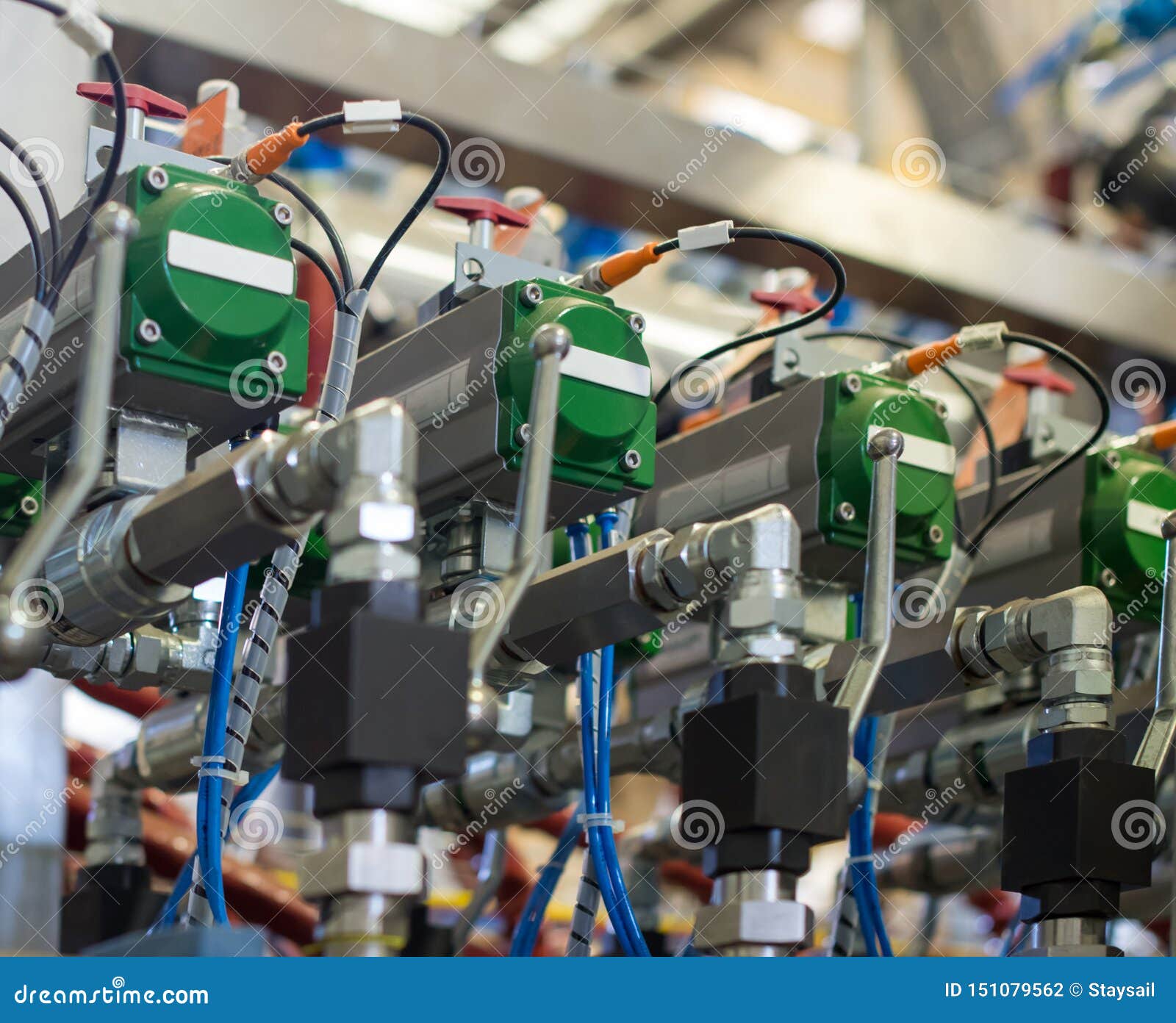
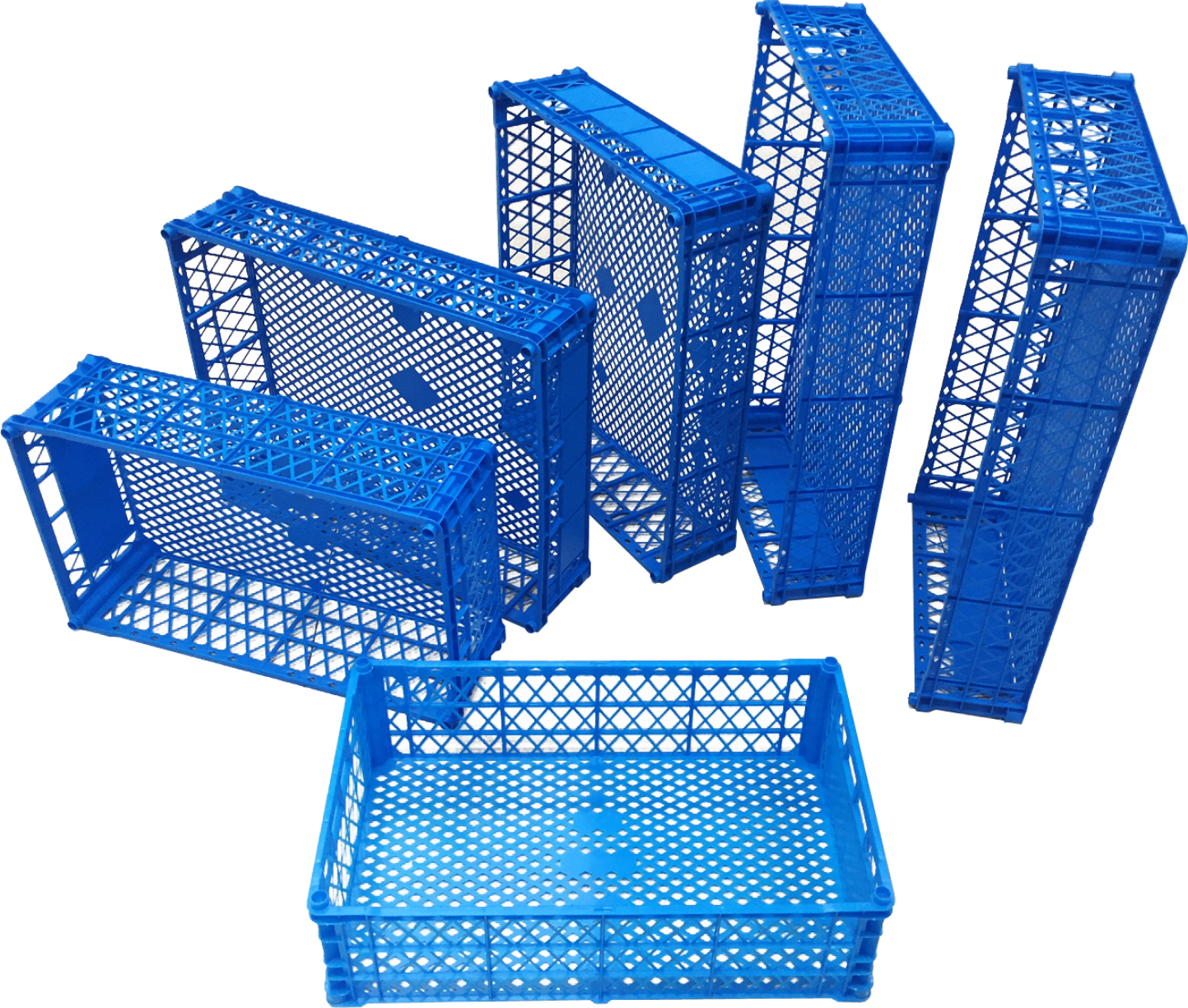

Detail Author:
- Name : Maverick Herzog
- Username : ichamplin
- Email : ebony.padberg@white.info
- Birthdate : 1986-03-02
- Address : 74971 Jakob Ridge Suite 789 New Genovevaland, CT 81783
- Phone : 563.815.3502
- Company : Nikolaus LLC
- Job : Dot Etcher
- Bio : Consequatur qui nemo et quo quo expedita impedit. Quam perferendis ex voluptas omnis fugit eveniet ratione. Molestiae tempore architecto vel recusandae itaque consequuntur.
Socials
linkedin:
- url : https://linkedin.com/in/althea_ritchie
- username : althea_ritchie
- bio : Veniam impedit aliquid necessitatibus eaque id.
- followers : 4572
- following : 2220
instagram:
- url : https://instagram.com/althearitchie
- username : althearitchie
- bio : Quos porro ullam nam. Qui voluptatem dolore dolore. Saepe velit eius tempora aut placeat.
- followers : 4950
- following : 134
twitter:
- url : https://twitter.com/althearitchie
- username : althearitchie
- bio : Omnis quas nihil ipsa aut et autem consequatur. Tempora occaecati eligendi alias suscipit.
- followers : 803
- following : 858
tiktok:
- url : https://tiktok.com/@althearitchie
- username : althearitchie
- bio : Consequatur et autem officiis est aut consequatur.
- followers : 4673
- following : 52